KEN'S KORNER - Relocating a Data Center
Tips on Relocating a Data Center
[caption id="attachment_177" align="alignright" width="172"]
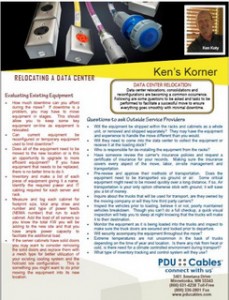
Data center relocations, consolidations and reconfigurations are becoming a common occurrence. Making sure your next move isn’t a painful experience requires a lot of thoughtful planning and precise implementation. Executing a seamless data center server room move involves coordinating transportation, labor, and on-site management.
Following are some questions to be asked and tasks to be performed to successfully facilitate your next move.
Evaluating Existing Equipment
• How much downtime can you afford during the move? If downtime is a problem, you may have to move equipment in stages. This should allow you to keep some key equipment on-line as equipment is relocated.
• Can current equipment be reconfigured or temporary equipment used to limit downtime?
• Does all of the equipment need to be moved to the new location or is this an opportunity to upgrade to more efficient equipment? If you have equipment that needs to be replaced, there is no better time to do it.
• Inventory and make a list of each piece of equipment giving it a name. Identify the required power and IT cabling required for each server and rack.
• Measure and log each cabinet for footprint size, total amp draw and number and type of power feeds (NEMA number) that run to each cabinet. Add the load of all servers so you know the total KW you will be adding to the new site and that you have ample power capacity to facilitate the additional load.
• If the server cabinets have solid doors you may want to consider removing the solid doors and replace them with a mesh type for better utilization of your existing cooling system and the hot/cold isle configuration. This is something you might want to do prior moving the equipment into its new location.
Questions to ask Outside Service Providers
• Will the equipment be shipped within the racks and cabinets as a whole unit, or removed and shipped separately? They may have the equipment and experience to handle the move different than you would.
• Will they need to come into the data center to collect the equipment or receive it at the loading dock?
• Who is responsible for de-installing the equipment from the racks?
• Have someone review the carrier’s insurance policies and request a certificate of insurance for your records. Making sure the insurance covers every aspect of the move, labor, on-site management and transportation.
• Pre-review and approve their methods of transportation. Does the equipment need to be transported via ground or air. Some critical equipment might need to be moved quickly over a long distance, if so, Air transportation is your only option otherwise stick with ground; it will save you a lot of money.
• Inquire about the trucks that will be used for transport, are they owned by the moving company or will they hire third party carriers?
• Inspect the vehicles prior to loading, believe it or not, poorly maintained vehicles breakdown. Though you can’t do a full checkup, a quick visual inspection will help you to sleep at night knowing that the trucks will make it to their destination.
• Monitor the equipment as it is being loaded into the trucks and inspect to make sure the truck doors are secured and locked prior to departure.
• Will security accompany the equipment throughout the move?
• Extreme temperatures are not uncommon in the back of trucks depending on the time of year and location. Is there any risk from heat or cold, is there need for a climate controlled environment during transport?
• What type of inventory tracking and control system will they use?
Preparing Space for New Equipment
• The orientation and relocation of old equipment into a new facility almost always requires new branch circuit power whips and data cables. Make sure the cable colors are consistent with pre-established coding schemes and cable management plans.
• If any of the power feeds have a straight blade connector change them to the locking type prior to energizing them in your new site.
• Know your electrical and cooling load prior to the move to ensure that the new site can handle the added load, and don’t forget to factor in for future growth.
• Be sure the PDU/RPP has amble capacity for dual corded server cabinets for fail over. This will not only ensure increased uptime but will allow you to shut down one critical path for maintenance without shutting down your servers.
• Using the total amps load, calculate your cooling capacity by converting KW to BTU’s. Calculate what the total heat load of cooling you will add to the new site. 1 Watt = 3.41 BTU’s and 12,000 BTU’s equal one ton of cooling.
• Meet with IT and layout new equipment in relation to existing equipment, server cabinets, PDU/RPPs. It is best if you have a drawing of the data center with its existing equipment identified.
• Use a grid system for the data center raised floor showing each floor tile with its own unique address. When creating an equipment layout consider which PDU/RPP’s will be used to feed the new servers. You want to minimize the length of the power runs and also take into account the IT cabling required to be installed. Be sure the new equipment will not affect your hot/cold aisle configuration.
• Pre-install all the power whips required for each server cabinet along with a brush grommet for the floor penetrations. A simple way to prepare the raised floor to receive the equipment is to follow the grid system and place waste paper baskets with a label on each identifying the piece of equipment to be installed at that spot. This makes installation quick and easy without any confusion. (SEE PICTURE BELOW)
Who is responsible for moving equipment?
• Identify who will pack and ship the equipment to the new location? Is this to be handled internally or outsourced? Included in this is identifying who’s responsibility it is to disconnect and disassemble the equipment.
• Don’t forget reassembly and reconnecting the equipment at the new location. It is a lot easier to disconnect than it is to reconnect. Where you can get by having less experienced people help disconnect equipment, it’s always advisable to have your best people handle the computer room equipment installation.
Ken Koty,