KEN'S KORNER - Commissioning with Load Banks
Commissioning with Load Banks
[caption id="attachment_196" align="alignright" width="173"]
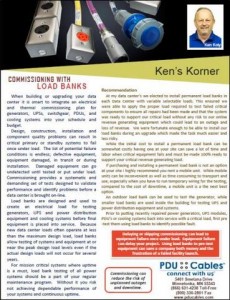
Commissioning is defined by the American Society of Heating, Refrigerating, and Air Conditioning Engineers (ASHRAE) as a quality-oriented process for achieving, verifying, and documenting that the performance of facilities, systems and assemblies meets the defined objectives and criteria.
When building or upgrading your data center it is smart to integrate an electrical and thermal commissioning plan for generators, UPSes, switchgear, PDUs, and cooling systems into your schedule and budget.
Design, construction, installation and component quality problems can result in critical primary or standby systems to fail once under load. The list of potential failure conditions is endless; defective equipment, equipment damaged, in transit or during installation. Damaged equipment can go undetected until tested or put under load. Commissioning provides a systematic and demanding set of tests designed to validate performance and identify problems before a data center is brought on-line.
Load banks are designed and used to create an electrical load for testing generators, UPS and power distribution equipment and cooling systems before final equipment is placed into service. Because new data center loads often operate at less than the maximum design load, load banks allow testing of systems and equipment at or near the peak design load levels even if the actual design loads will not occur for several years.
For mission critical systems where uptime is a must, load bank testing of all power systems should be a part of your regular maintenance program. Without testing, you risk not achieving dependable performance of your systems and continuous uptime.
Recommendation
At my data center’s, we elected to install permanent load banks in each data center with variable selectable loads. This ensured we were able to apply the proper load required to test failed critical components to ensure all repairs had been made and that the system was ready to support our critical load without any risk to our online revenue generating equipment which could lead to an outage and loss of revenue. We were fortunate enough to be able to install our load banks during an upgrade which made the task much easier and less risky.
While costly to install a permanent load bank, having one at your site can save a lot of time and labor when critical equipment fails and must be made 100% ready to support your critical revenue generating load.
If purchasing and installing a permanent load bank is not an option, I highly recommend you rent a mobile unit. While mobile units can be inconvenient as well as time consuming to transport and use, especially when you have to run temporary wiring for the testing, compared to the cost of downtime, a mobile unit is a the next best option.
An outdoor load bank can be used to test the generator, while smaller load banks are used inside the building for testing UPS and power distribution equipment and systems.
Prior to putting recently repaired power generators and cooling systems back into service with a critical load, first commission them using load banks to identify possible fault.
Delaying or skipping commissioning can lead to equipment failure once under load. Equipment failure can delay your project. Using load banks to pre-test equipment can save a company both money and the frustration of a failed facility launch.
Commissioning can reduce the risk of unplanned outages and downtime.
Load Bank Types
Load banks come in various types:
- Resistive
- Reactive
- Resistive/Reactive
Resistive being the most common type, the resistive load bank is created by the conversion of electrical energy to heat by power resistors. This heat must be dissipated from the load bank, either by air or water.
Types of resistive load banks:
• DC portable, smaller and easily carried or pushed on wheels for testing and maintaining DC power equipment like battery chargers, battery systems, UPS systems and DC generators.
• AC small portable units that can be carried or pushed on wheels which are used to test power equipment like UPS systems up to 100 KW.
• AC large portable load banks on wheels for testing and maintaining larger AC power equipment like UPS systems and generators up to 1000 KW.
• AC trailer mounted for testing power equipment up to 3000 KW
• AC stationary a resistive load bank for testing and maintaining power equipment up to 3000KW
• AC water cooled resistive load bank for testing and maintaining power equipment using water instead of air for cooling he resistive load elements. This type is much better for environments requiring a more quiet operation and are available up to 2500KW
Reactive load banks would be used on loads such as inductive (lagging power factor) and or (leading power factor loads).
Inductive loads, the more common type, consist of iron-core reactive elements which, when used in conjunction with a resistive load bank, create a lagging power factor load. Typically, the inductive load will be rated at a numeric value 75% that of the corresponding resistive load, such that when applied together, a resultant 0.8 power factor load is provided. That is to say, for each 100KW of resistive load, 75KVAR of inductive load is provided. These reactive load banks are typically available up to 1875 kVAR
Resistive/Reactive combine both resistive and reactive elements in one load bank package and are typically available up to 6250 KW.
Recommendation
There are a number of companies that both rent commissioning load banks as well as provide load bank service to help you commission your mission critical systems.
While performing these load tests Infra-Red (IR) scan each individual component of the system to identify any issues that need correcting before the system is brought on-line.
During load tests, while each individual component is under load, the system should be scanned with an IR scanner to find any issues and correct them long before your system is supporting your critical online revenue.
I would also recommend having a representative from each equipment manufacturer you are purchasing from visit your site and hold operation and safety classes for your entire staff on each individual component. This should include items such as UPS systems, batteries, diesel generators, switchgear, CRAC/CRAH units, cooling towers, proper cooling systems chemical treatment, fire detection systems and EPO systems. You should consider making a Video of each of these instructional classes, and make them available to all of your staff for training and instructional purposes. I did this and created a set of DVD’s that was assigned to everyone on my team. This will make a great reference for future. Remember there is a lot of information being shown and it can easily be forgotten as time goes by.
Ken Koty